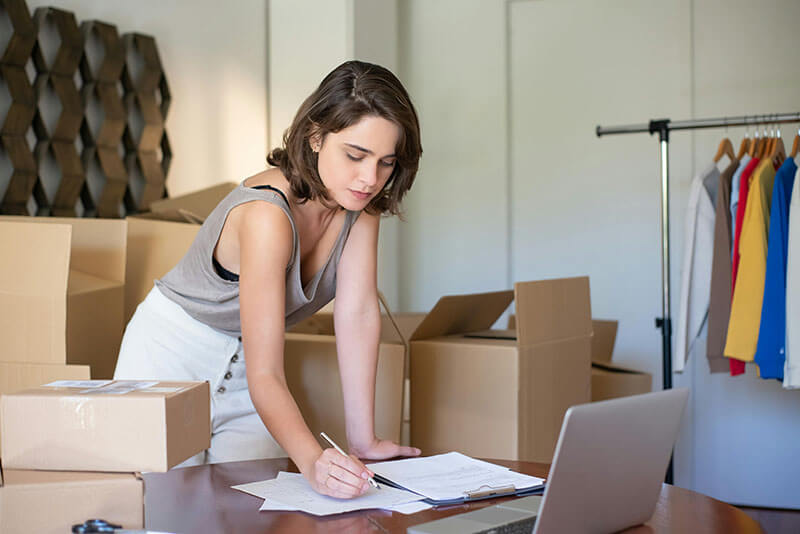
- The core formula, Beginning Inventory = (COGS + Ending Inventory) – Purchases, is essential for accurately determining the value of inventory at the start of an accounting period.
- Ensuring the accuracy of COGS, ending inventory, and purchase records is paramount for reliable beginning inventory calculations and overall financial health.
- Utilizing inventory management software and techniques, such as physical counts and barcode systems, significantly enhances accuracy and efficiency in tracking and calculating beginning inventory, especially across multiple warehouses.
- How to Find Beginning Inventory
- What Is the Beginning Inventory Formula?
- What Is Beginning Inventory?
- What Tools Can Help Calculate Beginning Inventory?
- What Is an Example of Beginning Inventory?
- Why Is Beginning Inventory Important?
- How to Find Beginning Inventory When Using Multiple Warehouses
- Where to Find Beginning Inventory on Financial Statements?
- How Do I Find My Missing Beginning Inventory?
- What if There Is No Beginning Inventory?
- How to Use Inventory to Calculate COGS?
- How to Find The Beginning Work in Process Inventory?
- Frequently Asked Questions About How to Find Beginning Inventory
How to Find Beginning Inventory
To find a beginning inventory, you must use a formula that shows the cost of goods sold (COGS), the value of purchases made, and the ending inventory from the last period. That is:
Beginning inventory = (COGS + Ending inventory) – Purchases
This provides the value at the start of the accounting period, which should match the information on the last period’s ending inventory. That means the starting period of the inventory should match the last ending inventory. This is crucial when maintaining financial records and reporting, thus ensuring gross profit.
What Is the Beginning Inventory Formula?
The beginning inventory formula is:
Beginning inventory = (COGS + Ending inventory) – Purchases
This helps ensure that the value at the beginning of the entry is the same as the value at the end of the accounting period. Each piece of information provided in the formula is crucial to calculating the beginning of the inventory.
- The cost of goods sold (COGS) is the direct cost attained by the amount of goods sold.
- Purchases are the costs of goods bought during the accounting period. This was done to replenish inventory.
- Ending inventory is the end of the accounting period.
Step 1: Determine Your Cost of Goods Sold (COGS)
To determine the cost of goods sold (COGS), deciding on the metric that ties to the direct costs of producing goods sold by the business is essential. This would include materials and labor that were used in the production of the goods. However, this does not factor in expenses such as distribution costs and sales force. Therefore, it is essential to understand COGS because it helps businesses determine the production rate’s efficiency and financial health. It is necessary to identify the profits and margins. Thus, higher COGS would provide a lower profit. This tells how the business manages its labor and production processes.
There are a few ways to identify COGS. These methods are:
- First in, first out (FIFO). This is where the oldest items are sold first. FIFO helps to lower the rate of COGS and provide a higher income. This is done during periods when prices are rising.
- Last in, first out (LIFO) is when the latest item is sent out. However, when prices rise, LIFO generates a higher rate of COGS and lower income.
- Weighted average cost. This is used to calculate the average cost of a unit. It is done by dividing the total inventory by the number of units bought.
- Specific identification. This helps with unique items where certain costs are known.
By determining the accuracy of COGS, organizations can ensure pricing strategies, identify areas that need cost control, and improve profitability.
Step 2: Determine Your Ending Inventory
To determine ending inventory, a few strategies are implemented. They are:
- Calculating cost of goods sold (COGS). This is important to know the ending inventory.
- Using inventory valuation methods such as FIFO, LIFO, or weighted average costs.
- Tracking inventory movements to ensure ending inventory.
- Performing regular physical counts ensures that the data aligns with the inventory records at hand. This would reduce the rate of inaccuracies and discrepancies.
- Utilizing inventory tracking software to ensure tracking and calculating the end inventory. This helps to enhance accuracy and efficiency.
- Analyzing inventory trends so businesses can forecast demands, adjust their buying power, and optimize the stock at hand.
Having an up-to-date ending inventory is crucial to ensure proper financial reporting, budgeting, and sales forecasts.
Step 3: Determine Your Purchases
Tracking and recording inventory levels is vital to determine your purchases of goods or raw materials. This is because the purchases play a role in the beginning inventory, increasing the inventory value when added to the stock at hand. To track and record purchases, businesses should:
- Implement a barcode system to track and record items.
- Ensure that there are regular cycle counts. This helps ensure the accuracy of the items and should be done daily or weekly. It also helps reduce discrepancies and ensures that the information is current.
- Use web based inventory software to automate and track manual tasks. This reduces the rate of errors and ensures that the inventory and financial statements match.
- Organize records. This is important to ensure the accuracy of information for financial reporting and inventory management.
- Prepare to receive the return of goods and provide discounts. These adjustments should be made to ensure that inventory levels are current.
These steps are important to ensure that businesses track and record their purchases.
What Is Beginning Inventory?
Beginning or opening inventory is the number of items the company has not sold. This value and information are then added to the start of the fiscal year’s or accounting period. These items must be sold, used, or carried forward from the ending inventory of the last accounting period.
This calculation ensures the beginning inventory at the start of the fiscal period.
(Cost of goods sold (COGS) + Ending inventory) – Inventory purchases.
This calculation shows the inventory at the beginning of the new fiscal period. This would factor in the assumption there are no inventory write-offs or down. The difference between beginning and ending inventory is the time of the fiscal period. Beginning inventory is the amount of inventory at the beginning period. The ending inventory is the value of the inventory at the end of the fiscal period.
What Tools Can Help Calculate Beginning Inventory?
Tools that help calculate beginning inventory are important when managing and calculating it. This ensures that records and stock levels are accurate while reducing errors and enhancing inventory management processes. Inventory management solutions often provide tracking capabilities, monitor reorder points, and generate reports. They can also include barcode scanning capabilities, enhancing accuracy and inventory counting.
The benefits of using an inventory calculator are reducing human error, processing large amounts of information, tracking stock levels, and generating reports and analytics. Therefore, Timly is designed to provide real-time inventory tracking, set up alerts if inventory levels fall below a certain level, generate reports, provide a customized dashboard, integrate with other accounting and e-commerce platforms such as ERP, enhance management practices, and reduce costs.
What Is an Example of Beginning Inventory?
An example of beginning inventory for a company that sells headbands. At the end of the accounting period, the company had 100 headbands left. Each of these costs around $15. Moreover, the company purchased another 400 headbands to add to the previous stock. They managed to sell around 1,000 headbands in the last period and had a cost of goods sold (COGS) of $15,000.
The formula is therefore calculated as:
- (COGS + Ending Inventory) – Purchases
The beginning inventory would be:
- Beginning inventory = ($15,000 + $1,500) – $6,000
- Beginning inventory = $10,500.
Why Is Beginning Inventory Important?
Beginning inventory is essential to determining the cost of goods sold (COGS) and its impact on the financial statements and profits. Therefore, accurate beginning inventory records are necessary to ensure that the total assets and equity are shown on the balance sheet. As for profitability, the beginning inventory is vital to calculating COGS. This impacts the gross profit margin, as COGS must be subtracted from revenue to determine profit.
Beginning inventory in the supply chain is vital to ensure optimal stock levels. It helps balance inventory levels to reduce the rate of stockouts and excess inventory, which can reduce the risk of missing sales and increase storage costs. As for tax reporting, beginning inventory impacts taxable income because it is used to determine COGS. Therefore, it is important to ensure proper inventory valuation to lower taxable income and reduce tax liability. As for business valuation, beginning inventory is important as it shows a part of the company’s total assets. It is vital to properly evaluate the beginning inventory to ensure that the overall asset value is correctly stated. This is important to ensure the fair market value for business.
How to Find Beginning Inventory When Using Multiple Warehouses
When using multiple warehouses, it is important to employ the proper strategy to determine beginning inventory. One challenge is to ensure that inventory records are accurate across all platforms. Thus, inaccuracy will cause stockouts, overstocking, and issues impacting orders and customer satisfaction.
Therefore, it is essential to consolidate inventory data from different warehouses. This system tracks inventory levels across all locations and provides a complete view of inventory status. Key performance indicators (KPIs) such as order fulfillment times, accuracy rates, and inventory turnover are essential for determining improvement areas.
Businesses should choose various inventory methods, such as FIFO, LIFO, weighted average costs, and specific assigned values. This helps determine the impact on finances and tax implications. Therefore, implementing a robust inventory system to manage inventory across multiple warehouses is essential. It would ensure features such as automated inventory management and standard processes and train staff to handle many tasks efficiently.
The Timly Software in Use
Optimized Device Management With Innovative Self-Inventory
SodaStream is the world market leader for water sparkling systems for domestic use and has a lot of IT equipment at its various locations. Many colleagues now work from their home offices. A digital solution for the efficient management of IT end devices became necessary...
Panasonic x Timly: Driving Technological Innovation
One of the most remarkable aspects of human ingenuity is our ability to innovate. Innovation is embedded in the DNA of consumer electronics giant Panasonic, which has diversified into a number of sectors, from heavy industry to construction...
Manage Video Equipment Efficiently Without Much Effort
The Hamburg media company always does outstanding journalistic work and is characterized by independent reporting. In order to maintain journalistic quality, the teams work with highly specialized devices – these need to be managed efficiently...
Smart City Asset Management – Timly in Use at DIGOOH
The core business of DIGOOH Media GmbH in Cologne is to manage digital city light posters (DCLP) for outdoor use in various cities in Germany. The challenge here lies in making the client’s communication message always available at the right time, in the right place...
(No credit card required)
Where to Find Beginning Inventory on Financial Statements?
Beginning inventory can be found on the balance sheets and income statements. Here is how to locate and understand its importance.
- On the balance sheet, the beginning inventory can be seen under the current assets section.
- The beginning inventory for the current period is similar to the ending inventory of the last fiscal period.
The importance of reviewing balance sheets and income statements is that:
- Balance sheets show a snapshot of the company’s financial position.
- The income statement shows the company’s financial performance for a certain period.
How Do I Find My Missing Beginning Inventory?
If the beginning inventory records are lost or you are not able to find them, you can:
- Use historical information from the previous fiscal financial statements. This is particularly seen in the balance sheets.
- Identify the cost of goods purchased during that period by looking at supplier invoices and purchase receipts records.
- Calculate the cost of goods during the period with the estimated beginning inventory.
- Determine the ending inventory using the gross profit method. This would involve using the COGS based on historical gross profit percentages and subtracting it from the cost of goods available for sale.
- Do a physical inventory count to ensure a precise figure for the ending inventory.
What if There Is No Beginning Inventory?
Without beginning inventory, a business can calculate costs using zero inventory and track purchases and sales from the beginning of operations. This helps to ensure that transactions are accounted for from the start. For businesses transitioning to a new accounting period, it is essential to adjust using the ending inventory of the last period as the beginning inventory.
New businesses that do not have any information can use COGS to calculate costs.
COGS= Beginning inventory + Purchases − Ending inventory
Since the beginning inventory is zero for a new business, the formula simplifies to:
COGS= Purchases − Ending inventory
This method helps calculate the cost of goods sold accurately and maintain financial records. For businesses transitioning to a new accounting period, it is crucial to ensure that the ending inventory of the previous period is correctly recorded as the beginning inventory of the latest period to maintain consistency in financial statements.
How to Use Inventory to Calculate COGS?
Using inventory to calculate COGS is vital to ensure that inventory is considered. Inventory adjustments are essential to reflect the state of the inventory and COGS. This can be done during the physical inventory count. It helps to correct any issues between recorded inventory and actual inventory levels. These adjustments could either increase or decrease COGS.
Different inventory methods, such as FIFO and LIFO, can impact COGS. Therefore, choosing a proper inventory method to maintain consistency in financial reporting is important. However, constantly switching methods can impact COGS by providing variations and affecting financial analysis and forecasting.
How to Find The Beginning Work in Process Inventory?
Work-in-process (WIP) inventory refers to partially completed goods that are still in manufacturing and not ready for sale. It is an essential part of how to improve inventory management and is seen as a current asset on the balance sheet. This potential for conversion into cash in a fiscal year reflects the value of WIP inventory. It is essential to use the WIP inventory value from the last accounting period to find the beginning of the WIP inventory. This is because the value is carried forward to the start of the new fiscal year.
The beginning WIP inventory is essential for calculating the current WIP inventory value using the formula:
Ending WIP inventory = Beginning WIP inventory + Manufacturing costs− Cost of Goods Manufactured (COGM)
This formula helps accurately determine the current WIP inventory value, which is necessary for effective inventory management and financial reporting.
Frequently Asked Questions About How to Find Beginning Inventory
How to Find Beginning Inventory When Using Multiple Warehouses?
When using multiple warehouses, it is important to employ the proper strategy to determine beginning inventory. One challenge is to ensure that inventory records are accurate across all platforms. Thus, inaccuracy will cause stockouts, overstocking, and issues impacting orders and customer satisfaction. Therefore, it is essential to consolidate inventory data from different warehouses. This system tracks inventory levels across all locations and provides a complete view of inventory status. Key performance indicators (KPIs) such as order fulfillment times, accuracy rates, and inventory turnover are essential for determining improvement areas.
Where Is Beginning Inventory Located?
Beginning inventory can be found on the balance sheets and income statements. Here is how to locate and understand its importance.
- On the balance sheet, the beginning inventory can be seen under the current assets section.
- The beginning inventory for the current period is similar to the ending inventory of the last fiscal period.
Recommended for you:
Book an online demo - free and without obligation - or create your free trial account directly.