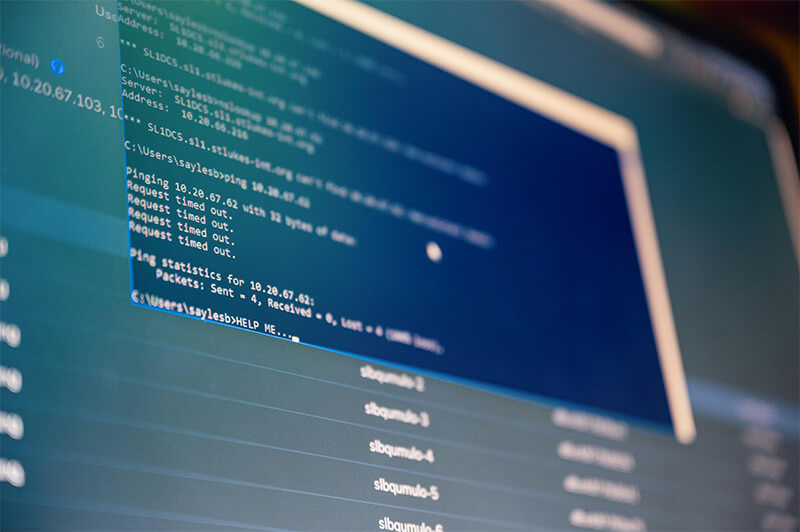
Key Takeaways:
- Computerized Maintenance Management Systems (CMMS) are databases that streamline maintenance operations by providing information on work orders, inventory management, preventive maintenance, and asset tracking.
- CMMS offers benefits such as automating tasks and workflows, reducing costs, and improving data management through a centralized platform.
- Selecting the right CMMS software involves identifying business requirements, evaluating features and scalability, considering costs and user interface, and verifying security and integration capabilities.
In This Article:
- What Is a Computerized Maintenance Management System?
- How Do Computerized Maintenance Management Systems Work?
- What Are the Benefits of Choosing a CMMS Program?
- What Are the Advantages Of CMMS Compared to Preventive Maintenance?
- Asset Management Software in Use by Our Customers
- How to Select the Right CMMS Software
- Is CMMS Implementation a Challenging Experience for Businesses?
- Cost Analysis of a CMMS Program
- Frequently Asked Questions About Computerized Maintenance Management System
What Is a Computerized Maintenance Management System?
A computerized maintenance management system (CMMS) is a database that holds and provides information about the maintenance operations of a business. This information effectively helps maintenance workers improve their work performance and assists stakeholders in making informed decisions about maintenance. Overall, it provides valuable data for work orders, inventory management, preventive maintenance, and asset tracking.
The purpose of using a CMMS is to help streamline maintenance operations, assist in reducing costs, and improve business efficiency when it comes to maintenance. It achieves this by allowing better planning, tracking, managing, and monitoring of maintenance performance and activities, which in turn help the business make better decisions.
What Is a Maintenance Management System Used For?
A maintenance management system (MMS) is a system that is used to assist businesses in managing and optimizing their maintenance operations. MMS is used to plan, schedule, track, monitor, and analyze the maintenance and performance of equipment. It is designed to make sure that there is proper maintenance being conducted on equipment and assets, which helps reduce operational downtime.
Many industries use CMMS, including:
Manufacturing Industry
The manufacturing industry uses CMMS to track and schedule maintenance activities so that downtime is reduced and production is maximized. Work orders are automated and the performance of equipment is monitored in order to determine if there are any rising issues, which helps with the overall costs.
Healthcare Sector
CMMS is widely used in the healthcare sector for tracking medical equipment and maintenance, ensuring items are available when needed. It is also used to identify whether equipment is functioning and does not pose issues that could affect patient care.
A case study of CMMS implementation is Kings River Packing, a citrus company. Facing challenges with outdated operational and inventory management systems, the company decided to upgrade to a centralized CMMS solution. This upgrade enabled Kings River Packing to efficiently manage inventory, work orders, preventive maintenance, and other equipment, significantly boosting productivity and resulting in annual savings of up to USD 500,000.
How Do Computerized Maintenance Management Systems Work?
What Are the Features of CMMS Maintenance?
The features of CMMS maintenance can be divided into three categories:
- Asset Management: helps to manage assets and provide location tracking, status of the asset, and its previous maintenance logs. This helps with the prioritization of tasks that will help with the maintenance of the asset.
- Work Order System: The system is designed to have work orders that will help with the assigning of tasks to dedicated technicians. This work order is then updated as the task is either in progress or completed.
- Predictive Maintenance: Data and analytics are used to identify the right time to schedule maintenance for an asset. This helps to reduce any unwanted downtime.
Over 600 Companies, Schools and Cities Rely on Timly
(No credit card required)
What Are the Benefits of Choosing a CMMS Program?
Choosing a CMMS program brings many benefits to your organization. Here are some of the advantages:
- Automate tasks and workflows, which help streamline the tracking of maintenance processes. Moreover, you will have real-time visibility on its status and be able to provide predictive maintenance, which helps reduce downtime.
- It also helps to reduce the costs of manual tasks, downtime, inventory management software costs, and energy consumption by optimizing maintenance and reducing overall waste.
- Provides management of data through a centralized platform, which helps improve compliance, collaboration, and accessibility of information for teams and stakeholders.
Implementing a CMMS can yield significant cost savings. For example,, a food processing plant reported a 400% increase in work order completion rates after adopting a CMMS. Similarly, a Texas school district saw a dramatic improvement in maintenance visibility, going from 0% to 100%. These examples highlight the potential for substantial efficiency gains and cost reductions through the adoption of a CMMS.
What Are the Advantages Of CMMS Compared to Preventive Maintenance?
The advantages of CMMS compared to preventive maintenance are that, while preventive maintenance is important to ensure assets are reliable and efficient, it can be time-consuming and prone to human error. CMMS streamlines preventive maintenance by automating tasks such as scheduling maintenance on a regular basis, tracking the status of work orders, and providing reminders for upcoming tasks. It also enables real-time monitoring of assets, which can aid in prolonging the lifespan of equipment.
Asset Management Software in Use by Our Customers
The Timly software is continuously evolving to meet the needs of our customers. In various success stories, we show you how Timly optimizes processes in companies, thereby saving significant effort. With Timly, inventory management becomes child’s play.
Optimized Device Management With Innovative Self-Inventory
SodaStream is the world market leader for water sparkling systems for domestic use and has a lot of IT equipment at its various locations. Many colleagues now work from their home offices. A digital solution for the efficient management of IT end devices became necessary...
Panasonic x Timly: Driving Technological Innovation
One of the most remarkable aspects of human ingenuity is our ability to innovate. Innovation is embedded in the DNA of consumer electronics giant Panasonic, which has diversified into a number of sectors, from heavy industry to construction...
Manage Video Equipment Efficiently Without Much Effort
The Hamburg media company always does outstanding journalistic work and is characterized by independent reporting. In order to maintain journalistic quality, the teams work with highly specialized devices – these need to be managed efficiently...
Smart City Asset Management – Timly in Use at DIGOOH
The core business of DIGOOH Media GmbH in Cologne is to manage digital city light posters (DCLP) for outdoor use in various cities in Germany. The challenge here lies in making the client’s communication message always available at the right time, in the right place...
(No credit card required)
How to Select the Right CMMS Software
1. Evaluate features and functionalities of the software
2. Determine scalability of the software
3. Assess implementation and support options
4. Review pricing and cost structure
5. Request trial or demo session
6. Confirm security and compliance measures
7. Explore software integration capabilities
8. Verify mobile accessibility options
Comparing Top CMMS Solutions
When choosing a CMMS, it is important to evaluate solutions based on a number of criteria. Let’s Look at some of the key things to consider:
- Assess the software’s functionality and determine whether it offers features such as work order and inventory management, asset tracking, and reporting capabilities.
- Consider scalability and ensure the software can scale as your business grows. Verify what the pricing will look like if you add more features to your packages as your company scales.
- Test the user interface to make sure it is reliable, simple to use, and easy for the maintenance team to understand.
- Evaluate the full cost of the solution and its implementation.
- Enquire about the level and type of customer support.
- Evaluate mobile access capabilities.
- Check security features such as access control, data encryption, and backup.
- Identify CMMS’s ability to customize according to business needs.
- Access the reporting and analytics and determine if it is able to generate key performance index (KPI) capabilities.
Now that we’ve looked at what to consider when comparison the best CMMS solutions, let’s now turn our attention to some of the top providers:
- MaintainX is a CMMS software that provides workflow access with reporting and analytical capabilities.
- Fracttal n delivers a maintenance management solution for physical assets,has predictive maintenance and asset tracking capabilities.
- Timly’s CMMS provides a comprehensive asset tracking solution with features such as GPS tracking, mobile scanning, digital file management, and maintenance management.
Trial and Pilot Testing to Gain CMMS Skills
With every software implementation, it is important to conduct a trial or pilot phase to ensure that it is right for your unique needs and use case. . Here are a few key steps to consider when testing CMMS software:
- Outline the maintenance management software goals and objectives.
- Ensure that you are using a free trial or pilot phase software.
- Select a department to conduct the test.
- Assess the CMMS software features and determine if they are sustainable for the business.
- Identify a maintenance schedule that can be incorporated into the trial phase.
- Gather feedback from users and stakeholders to identify any bugs or issues that need to be addressed before full implementation.
Is CMMS Implementation a Challenging Experience for Businesses?
Yes, CMMS implementation can be a challenging experience for businesses. This is because around 70% of all CMMS implementations do not meet expectations and there are a few common issues that businesses face when implementing the software.
Here are some of the challenges that businesses face during implementation:
- Lack of top-down communication which causes implementation issues and failure.
- Without guided training, staff may not be able to use the CMMS software effectively.
- When implementing new technology, there will always be resistance to change. Therefore, it is important that employees are involved in the decision-making process.
- Lack of planning, combined with unclear objectives, may lead to implementation issues.
- If the software does not have proper data quality, businesses may experience inaccurate reporting, which leads to low-quality decision-making.
Here are some reasons why CMMS implementations may fail:
- Poor budgeting or lack of resources.
- There is no proper communication between stakeholders.
- Inadequate training.
- Not wanting to embrace changes in the business.
- No clear objectives.
In order to overcome potential failure, you will need to ensure that:
- Upper-level management is involved and support the CMMS implementation.
- In-depth training on the software is offered so that it is used effectively.
- Employees are included in the decision-making process.
- A detailed plan is developed that showcases project implementation, objectives, and timelines
- Implementation progress is monitored, and tweaks are made where needed
Cost Analysis of a CMMS Program
When it comes to the cost analysis of a CMMS program, it is important to note that there are a few key components involved in costing. A CMMS program typically requires several cost variables, such as upfront payment, maintenance of software, and training. Let us look at these breakdowns:
A comprehensive Computerized Maintenance Management System (CMMS) program involves various cost components, including upfront investment, ongoing maintenance, and comprehensive training. Here’s a breakdown of these costs:
- Upfront Payment: This refers to the initial cost of purchasing the CMMS software. This can range from a few hundred dollars to several thousand dollars.
- Maintenance Cost: Covers the ongoing expenses for maintaining the software, including bug fixes, updates, and technical support.
- Training Cost: With any new software implementation, training is crucial for ensuring that staff can use the system effectively.
Is It Worth Investing in a Computerized Maintenance Management System?
Here is a case study and example of a successful ROI achievement:
ABC Corp. achieved a positive ROI by reducing unnecessary breakdowns and associated costs. This resulted in annual savings of USD 2000. Furthermore, by extending the lifespan of their assets, they lowered their inventory management software cost,leading to savings of USD 3,500 per annum.
Frequently Asked Questions About Computerized Maintenance Management System
What Is a Computerized Maintenance Management System?
How to Select the Right CMMS Software
It is important to understand that CMMS is crucial for businesses that focus on maintenance and asset management. There are many providers out there and it can be daunting to select
the right type of CMMS for your business. Factors to consider when choosing the right solution include:
- Features and functionalities of the software.
- Scalability of the solution.
- Implementation and support options.
- Cost and pricing structure.
- Availability of a free product demo or trial.
- Security and compliance aspects.
- Software integration capabilities.
- Mobile accessibility.
Recommended for You:
Book an online demo - free and without obligation - or create your free trial account directly.