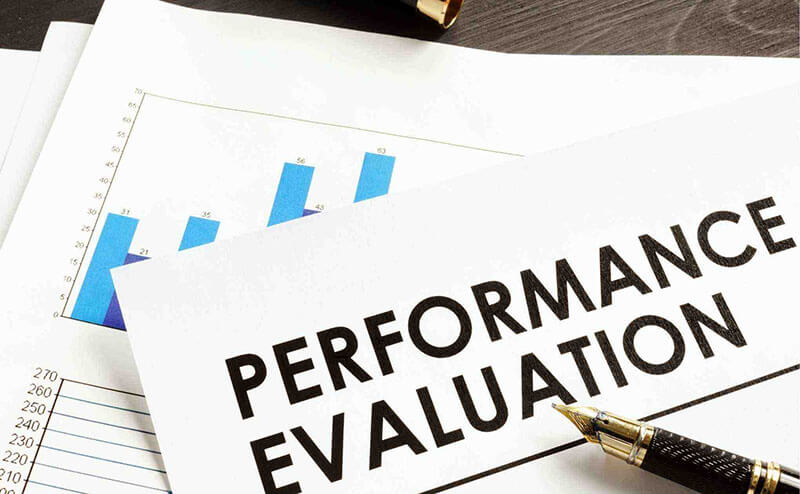
Wesentliche Erkenntnisse:
- OEE misst die Anlageneffizienz anhand von Verfügbarkeits-, Leistungs- und Qualitätskennzahlen.
- Es identifiziert Ineffizienzen wie Ausfallzeiten, langsame Zyklen oder Qualitätsmängel.
- OEE hilft bei der Rationalisierung von Arbeitsabläufen, der Reduzierung von Verschwendung und der Steigerung der betrieblichen Effizienz.
- Ein OEE-Wert von Weltklasse liegt bei 85 %, was eine optimale Fertigungseffizienz bedeutet.
- OEE unterstützt die Ziele der schlanken Produktion und der gesamten produktiven Instandhaltung.
Themen in diesem Beitrag:
- Gesamtanlageneffektivität
- Wie wird die Gesamtanlageneffektivität berechnet?
- Schritte zur Berechnung der Gesamtanlageneffektivität
- Was sind die Komponenten des OEE-Rahmens
- Was ist ein guter OEE-Wert und wie sollte er interpretiert werden?
- Wie können Sie die Gesamtanlageneffektivität verbessern?
- Praktische Anwendungen und Vorteile von OEE
- Wie können Sie die OEE effektiv messen und überwachen?
- Häufig gestellte Fragen zur Gesamtanlageneffektivität
Gesamtanlageneffektivität
Die Gesamtanlageneffektivität (Overall Equipment Effectiveness, OEE) ist eine wichtige Kennzahl in der Fertigung, die die Effizienz durch die Bewertung von drei Schlüsselfaktoren misst: Anlagenverfügbarkeit, Leistung und Qualität. Sie bietet eine standardisierte Kennzahl, um zu beurteilen, wie gut die Maschinen im Vergleich zu ihrer maximalen potenziellen Kapazität arbeiten.
OEE hilft dabei, spezifische Probleme zu identifizieren, die zu Ineffizienzen führen können, wie z. B. ungeplante Ausfallzeiten oder niedrige Produktionsgeschwindigkeiten. So können Unternehmen gezielte Maßnahmen ergreifen, um die OEE-Leistung zu erhöhen und die Gesamteffektivität der Anlagen zu steigern
Durch die Messung der OEE und die Analyse ihrer Komponenten können Hersteller daher ihre Arbeitsabläufe optimieren, Verschwendung reduzieren und ihre allgemeinen Betriebsziele erreichen.
Folglich spielt die OEE eine entscheidende Rolle für den Erfolg von Fertigungsprozessen. Sie ist ein unschätzbares Werkzeug für Hersteller, die ihre Effizienz und Rentabilität steigern wollen.
Wie wird die Gesamtanlageneffektivität berechnet?
Die Berechnung der Gesamtanlageneffektivität (Overall Equipment Effectiveness, OEE) umfasst die Analyse dreier grundlegender Komponenten, die sich direkt auf die Fertigungseffizienz auswirken. Zu diesen Komponenten gehören:
OEE = Availability x Performance x Quality
Jeder Faktor befasst sich mit einem bestimmten Aspekt der Anlageneffektivität. So misst beispielsweise die Verfügbarkeit die tatsächliche Betriebszeit. Die Leistung wiederum gibt an, ob die Anlagen mit ihrer maximalen Kapazität arbeiten oder nicht. Außerdem spiegelt die Qualität den Anteil der fehlerfreien Produkte im Verhältnis zum Gesamtausstoß wider
Die Messung der OEE ist für Hersteller von entscheidender Bedeutung, da sie ihnen hilft, Probleme wie unerwartete Ausfallzeiten, langsamer als optimale Produktionsraten oder Fehler, die die Produktqualität beeinträchtigen, zu erkennen
Wenn Sie die OEE-Leistung verstehen, können Sie gezielte Verbesserungen einführen, z. B. bessere Wartungspläne oder Anpassungen der Arbeitsabläufe. Dieser datengestützte Ansatz verbessert die betriebliche Effizienz, reduziert Verschwendung und unterstützt langfristige Produktivitätssteigerungen.
Stellen Sie sich beispielsweise vor, eine Maschine hat eine geplante Laufzeit von 720 Minuten, war aber 600 Minuten lang in Betrieb, was zu einem Ergebnis führt:
Availability = 83.3%
Während dieser Zeit wurden 1.000 Einheiten mit einer Rate von 83,3 % der Höchstgeschwindigkeit produziert (Leistung = 83,3 %), und 900 dieser Einheiten waren fehlerfrei (Qualität = 90 %). Die OEE-Berechnung würde also lauten:
0.833 x 0.833 x 0.9 = 62.5%
Das bedeutet, dass die Maschine nur mit 62,5 % ihres vollen Potenzials arbeitet. Das bedeutet, dass die Verfügbarkeit, die Leistung und die Qualität verbessert werden können.
Über 600 Firmen, Schulen und Städte vertrauen auf Timly
(Keine Kreditkarte notwendig)
Schritte zur Berechnung der Gesamtanlageneffektivität
Die Berechnung der Gesamtanlageneffektivität (Overall Equipment Effectiveness, OEE) umfasst die Auswertung von drei Schlüsselkennzahlen: Verfügbarkeit, Leistung und Qualität. Diese Komponenten messen zusammen, wie effektiv die Fertigungsanlagen während der geplanten Produktionszeit arbeiten. Im Folgenden wird jeder Schritt im Detail erläutert.
Wie berechnet man die Verfügbarkeit in OEE?
Die Verfügbarkeit ist ein Maß dafür, wie viel der geplanten Produktionszeit die Anlagen tatsächlich in Betrieb sind. Sie hebt die Zeiträume hervor, in denen die Maschinen aufgrund von Problemen wie Ausfällen, Wartung oder Einrichten nicht arbeiten. Dies macht sie zu einer wichtigen Komponente der Gesamtanlageneffektivität (OEE).
Denn ohne hohe Verfügbarkeitszahlen können auch gut funktionierende Anlagen mit hoher Leistung nicht ihr volles Potenzial ausschöpfen, da die Betriebszeit begrenzt ist.
Die Formel für die Verfügbarkeit ist einfach, aber wirksam:
Availability = Actual Operating TIme / Planned Production Time x 100
Wenn zum Beispiel eine Maschine für 480 Minuten geplant ist, aber wegen ungeplanter Wartungsarbeiten nur 400 Minuten in Betrieb ist, beträgt die Verfügbarkeit (400 ÷ 480) × 100 = 83,3 %. Diese Zahl spiegelt wider, wie effektiv die Anlage während ihrer vorgesehenen Betriebszeit genutzt wird.
Um die Anlagenverfügbarkeit wirklich zu maximieren, müssen die Hersteller jedoch auch die Auswirkungen geplanter Ausfallzeiten auf die Produktion berücksichtigen. Sie können diese Verluste durch die Einführung von Strategien zur vorausschauenden Wartung verringern. Diese Strategien erkennen potenzielle Probleme, bevor sie zu Ausfällen führen.
Darüber hinaus kann die Rationalisierung von Einrichtungs- und Umrüstungsprozessen die Ausfallzeiten erheblich reduzieren und sicherstellen, dass die Anlagen einsatzbereit bleiben und den OEE-Effizienzzielen entsprechen. Dies führt letztendlich zu einer verbesserten Gesamteffektivität der Anlagen und einer höheren Rentabilität.
Das oben genannte Bild stammt von LinkedIn.
Wie berechnet man die Leistung in OEE?
Die Leistung ist eine entscheidende Komponente der Gesamtanlageneffektivität (Overall Equipment Effectiveness, OEE), da sie sich direkt auf die Produktionsraten und die Gesamteffizienz der Fertigung auswirkt. Die Leistungseffizienz bewertet, wie effektiv die Ausrüstung im Vergleich zu ihrer maximalen potenziellen Kapazität arbeitet. Diese Kennzahl identifiziert Geschwindigkeitsverluste, wie langsame Zyklen oder kurze Stopps, die eine optimale Produktivität behindern.
Die Formel zur Berechnung der Leistung ist einfach:
Performance = Ideal Cycle Time x Total Units Produce / Actual Operating Time x 100
Die Leistung kann in wenigen einfachen Schritten gemessen werden:
- Ermittlung der idealen Zykluszeit: Die ideale Zykluszeit ist die theoretische Mindestzeit, die zur Herstellung einer Einheit eines Produkts benötigt wird.
- Berechnen Sie die theoretische Produktionszeit: Sobald Sie die ideale Zykluszeit ermittelt haben, können Sie diese mit der Gesamtzahl der in einem bestimmten Zeitraum produzierten Einheiten multiplizieren, um die theoretische Produktionszeit zu erhalten.
- Vergleich mit tatsächlicher Betriebszeit: Teilen Sie die theoretische Produktionszeit durch die tatsächliche Betriebszeit, um die Leistungseffizienz zu berechnen. Auf diese Weise erhalten Sie einen Prozentsatz, der angibt, wie nahe Ihre Ausrüstung an ihrer maximalen potenziellen Kapazität arbeitet.
Abgesehen von diesen Schritten gibt es bestimmte gemeinsame Faktoren, die sich auf die Leistungsraten auswirken können und die für optimale Ergebnisse berücksichtigt werden müssen. Dazu gehören langsame Zyklen, kleine Pausen und Schwankungen in der Fachkompetenz der Bediener. Die Behebung dieser Faktoren ist also entscheidend für die Verbesserung der Leistung und der OEE.
Wie berechnet man die Qualität in OEE?
Die Qualität in der Gesamtanlageneffektivität (OEE) konzentriert sich auf den Anteil der fehlerfreien Produkte an der Gesamtproduktion. Sie bewertet, wie gut ein Fertigungsprozess Produkte liefert, die den Qualitätsstandards entsprechen. Sie zeigt auch Bereiche auf, in denen Verschwendung minimiert werden kann.
Diese Komponente ist auch für die Maximierung der Effizienz von entscheidender Bedeutung, da fehlerhafte Waren einen hohen Ressourcenverbrauch verursachen, ohne zu einer verwertbaren Produktion beizutragen. Beispielsweise können fehlerhafte Artikel eine zusätzliche Bearbeitung erfordern, was die Produktionszeiten verlängert und die effektive Nutzung der Anlagen verringert. Dies senkt direkt die Produktivität und Rentabilität.
Die Formel für die Berechnung der Qualität ist ganz einfach:
Quality = Number of Defect Free Units / Total Number of Units Produced x 100
Sie können es in einigen einfachen Schritten messen:
- Ermitteln Sie zunächst den gesamten Produktionsausstoß in einem bestimmten Zeitraum.
- Erfassen Sie anschließend die Anzahl der Einheiten, die den Qualitätsstandards entsprechen.
- Teilen Sie dann die Anzahl der fehlerfreien Einheiten durch die Gesamtzahl der produzierten Einheiten und multiplizieren Sie mit 100, um den Qualitätsprozentsatz zu berechnen.
- Vergleichen Sie schließlich das Ergebnis mit Industriestandards oder früheren Leistungen, um Bereiche mit Verbesserungspotenzial zu ermitteln.
Was sind die Komponenten des OEE-Rahmens
Der Rahmen für die Gesamtanlageneffektivität (OEE) besteht aus drei Schlüsselkomponenten: Verfügbarkeit, Leistung und Qualität. Diese Komponenten werden multipliziert, um den OEE-Wert zu berechnen und Einblicke in die Anlagennutzung und Produktivität zu geben. Zum Beispiel:
- Verfügbarkeit: Diese Komponente misst den Prozentsatz der geplanten Produktionszeit, in der die Anlagen betriebsbereit sind. Sie berücksichtigt alle Ausfallzeiten aufgrund von Pannen, Wartung oder Rüstungsänderungen.
- Leistung: Die Leistungskomponente bewertet, ob die Ausrüstung mit ihrer maximalen Geschwindigkeit arbeitet, indem die tatsächliche Leistung mit der idealen Zykluszeit verglichen wird. Sie zeigt auch Verluste durch langsame Zyklen oder kleinere Stopps auf.
- Qualität: Mit dieser Komponente wird der Anteil der fehlerfreien Produkte bewertet und die durch Fehler und Nacharbeit verursachte Verschwendung ermittelt.
Jede Komponente spielt eine entscheidende Rolle bei der Verbesserung der Anlageneffizienz und der Minimierung von Ausschuss. Die Erhöhung der Verfügbarkeit verringert zum Beispiel die Ausfallzeiten, die Optimierung der Leistung erhöht die Produktionsgeschwindigkeit und die Verbesserung der Qualität minimiert fehlerhafte Ergebnisse.
Zusammengenommen ermöglichen es diese Messgrößen den Herstellern, Ineffizienzen systematisch anzugehen und die Gesamteffizienz der Anlagen zu verbessern.
Dieses Bild wurde von Evocon übernommen. Es zeigt eine interaktive Darstellung der OEE
Die obige Darstellung ist eine interaktive Darstellung der OEE, die häufig Diagramme oder Dashboards verwendet, um Echtzeitdaten für jede Komponente anzuzeigen. Dies hilft den Teams, den Fortschritt zu überwachen und verbesserungswürdige Bereiche zu identifizieren. Indem sie sich auf diese Echtzeitdaten konzentrieren, können Hersteller eine höhere OEE-Leistung erzielen und sich an den Zielen für die betriebliche Anlageneffizienz orientieren.
Die Timly Software in der Anwendung
Optimierte Inventarverwaltung mit innovativer Selbstinventur
SodaStream ist der weltweite Marktführer für Wassersprudelsysteme im Heimbereich und hat zahlreiche IT-Geräte an verschiedenen Standorten. Viele Kollegen arbeiten nun von ihren Home-Offices aus, weshalb eine digitale Lösung für das effiziente Management der IT-Endgeräte erforderlich wurde...
Panasonic & Timly: Technologische Innovation vorantreiben
Beim Unterhaltungselektronik-Giganten Panasonic, der in eine Reihe von Sektoren diversifiziert hat, von der Schwerindustrie bis zum Bauwesen, ist Innovation in der DNA verankert. Lesen Sie, warum sich Panasonic Industrial Devices Europe für die Inventarverwaltung mit Timly entschieden hat...
Video-Equipment effizient und mühelos verwalten
Das Hamburger Medienunternehmen liefert stets herausragende journalistische Arbeit und zeichnet sich durch unabhängige Berichterstattung aus. Zur Aufrechterhaltung der journalistischen Qualität müssen die Teams mit hochspezialisierten Geräten effizient arbeiten...
Smart City Asset Management – Timly im Einsatz bei DIGOOH
Die DIGOOH Media GmbH in Köln verwaltet digitale City-Light-Poster (DCLP) für den Außeneinsatz in verschiedenen deutschen Städten als Kerngeschäft. Die Herausforderung besteht darin, die Kommunikationsbotschaft des Kunden stets zur richtigen Zeit und am richtigen Ort verfügbar zu machen.
(Keine Kreditkarte notwendig)
Was ist ein guter OEE-Wert und wie sollte er interpretiert werden?
Ein guter Wert für die Gesamtanlageneffektivität (Overall Equipment Effectiveness, OEE) variiert je nach Branche. Ein OEE-Wert von 85% gilt in der Fertigung jedoch weithin als Weltklasse.
Denn 85% OEE stehen für einen gut optimierten Prozess, bei dem die Anlagen mit minimalen Ausfallzeiten arbeiten, mit effizienter Geschwindigkeit produzieren und qualitativ hochwertige Waren ausgeben
Um dieses Niveau zu erreichen, sind jedoch in der Regel strenge Prozesskontrollen, eine vorausschauende Wartung und solide Qualitätsmanagementverfahren erforderlich.
Im Folgenden finden Sie einige weitere Standard-Benchmarks, die zur Bewertung der OEE-Leistung verwendet werden:
- 85% oder höher: Weltklasse-Leistung. Sie zeigt einen hocheffizienten und optimierten Betrieb.
- 60%-85%: Gute Leistung. Dies kann mit einigen Anstrengungen zur Verbesserung der Verfügbarkeit, Leistung oder Qualität erreicht werden.
- 40%-60%: Durchschnittliche Leistung. Sie zeigt an, dass erheblicher Spielraum für Verbesserungen besteht, um Verluste zu minimieren.
- Weniger als 40%: Schlechte Leistung. Sie erfordert eine gezielte Strategie zur Beseitigung von Ineffizienzen und zur Steigerung der Produktivität.
Es ist jedoch wichtig zu wissen, dass sich die OEE-Werte je nach Branche aufgrund der besonderen Anforderungen der Produktionsprozesse unterscheiden. In solchen Branchen wie der kontinuierlichen Fertigung und der Lebensmittelverarbeitung werden oft höhere OEE-Werte erzielt, wobei 90% auf rationalisierte Arbeitsabläufe und konsistenten Output zurückzuführen sind
In der diskreten Fertigung, z. B. in Montagelinien für die Automobilindustrie, kann eine OEE von 75% akzeptabel sein, da häufige Umrüstungen und Produktanpassungen hier naturgemäß zu einer größeren Variabilität führen.
Das Verständnis dieser Unterschiede hilft den Herstellern, realistische Ziele entsprechend den Herausforderungen ihrer Branche zu setzen.
Wie können Sie die Gesamtanlageneffektivität verbessern?
Sie können die Gesamtanlageneffektivität (Overall Equipment Effectiveness, OEE) verbessern, indem Sie Ineffizienzen bei Verfügbarkeit, Leistung und Qualität ermitteln. Dann können Sie gezielte Strategien zur Beseitigung dieser Bereiche umsetzen.
Im Folgenden haben wir sechs effektive Strategien zur Verbesserung der OEE, potenzielle Herausforderungen und die Tools, die zum Erfolg führen können, beschrieben.
- Führen Sie eine vorbeugende und vorausschauende Wartung durch, indem Sie Routinekontrollen planen und Daten zur Vorhersage und Vermeidung von Ausfällen nutzen.
- Optimieren Sie die Produktionsplanung, um Arbeitsabläufe zu rationalisieren und die Umrüstzeiten mit Techniken wie SMED zu minimieren.
- Schulung der Bediener zur Verbesserung der Fähigkeiten, zur Reduzierung von Fehlern und zur Verbesserung der Maschinenauslastung.
- Nutzen Sie die Echtzeitüberwachung mit Tools wie Timly, um Ineffizienzen sofort zu erkennen und zu beheben.
- Umsetzung der Prozessoptimierung zur Beseitigung von Verschwendung und Engpässen und Verbesserung des Gesamtflusses.
- Konzentration auf die Qualitätskontrolle durch regelmäßige Audits und Qualitätsmaßnahmen, die eine fehlerfreie Produktion und weniger Abfall gewährleisten.
Hersteller stoßen häufig auf immer wiederkehrende Hindernisse, wie z. B. Ausfallzeiten von Anlagen, langwierige Umstellungen und uneinheitliche Qualitätsstandards. Diese Herausforderungen entstehen durch ungeplante Anlagenausfälle, verlängerte Rüstzeiten bei Produktwechseln und fehlerhafte Produkte. Die Bewältigung dieser Probleme erfordert jedoch einen strukturierten Ansatz und proaktive Maßnahmen.
Denn die Verfügbarkeit ist die Grundlage der OEE, und jeder Verlust in diesem Bereich kann sich auf die Leistungs- und Qualitätsmetriken auswirken. Die „Sechs großen Verluste“ in der Fertigung sind die Hauptursachen für Ineffizienzen bei Verfügbarkeit, Leistung und Qualität. Die Behebung dieser Verluste ist daher von entscheidender Bedeutung für die Verbesserung der OEE und die Beseitigung von Verschwendung. Zu den sechs Kategorien gehören:
- Ausfälle durch unerwartete Geräteausfälle, die die Verfügbarkeit verringern.
- Einrichtungs- und Einstellarbeiten, wie z. B. Umstellungen, unterbrechen den Betrieb und verringern die Betriebszeit.
- Kleine Unterbrechungen durch geringfügige Produktionsunterbrechungen oder Anpassungen, die Zeit kosten.
- Reduzierte Geschwindigkeit, wenn Maschinen unterhalb ihrer optimalen Geschwindigkeit arbeiten und die Leistung beeinträchtigen.
- Fehler, die zu Nacharbeit oder Abfall führen, schaden der Qualität unmittelbar.
- Anlaufverluste treten während der anfänglichen Produktions- oder Hochlaufphase auf und wirken sich auf alle drei OEE-Komponenten aus.
Wenn man diese Verluste versteht, ist es einfacher, gezielte Strategien umzusetzen. Die Software von Timly kann diesen Prozess auch unterstützen, indem sie detaillierte Einblicke in jede Verlustkategorie bietet. Mit den Softwarelösungen von Timly können Hersteller eine höhere OEE erreichen und so eine verbesserte betriebliche Anlageneffizienz und nachhaltiges Wachstum sicherstellen.
Praktische Anwendungen und Vorteile von OEE
Die Verfolgung der Gesamtanlageneffektivität (Overall Equipment Effectiveness, OEE) ist für Hersteller von großem Wert. Sie bietet verwertbare Erkenntnisse zur Verbesserung der Produktivität, zur Verringerung der Verschwendung und zur Maximierung der Anlagennutzung. Dies trägt insgesamt dazu bei, Produktionsengpässe zu beseitigen, ungeplante Ausfallzeiten zu reduzieren und die Produktqualität durch Minimierung von Mängeln und Abfall zu verbessern.
Das ist der Grund dafür, dass OEE durch die Erhöhung der Anlagenauslastung einen höheren Output ohne zusätzliche Ressourcen gewährleistet. Außerdem unterstützt sie die Skalierbarkeit, indem sie die betrieblichen Abläufe an die Anforderungen einer wachsenden Produktion anpasst.
OEE ergänzt auch die Ziele von Lean Manufacturing und Total Productive Maintenance (TPM). Durch die Beseitigung von Verschwendung und die Verbesserung der Zuverlässigkeit werden die betrieblichen Ziele mit den Prinzipien der kontinuierlichen Verbesserung in Einklang gebracht. Die Aufrechterhaltung einer konstanten OEE-Leistung gewährleistet beispielsweise kosteneffiziente Arbeitsabläufe und rationalisierte Produktionsprozesse.
Durch die Aufdeckung versteckter Ineffizienzen wie ungeplanter Ausfallzeiten oder langsamer Zyklen befähigt OEE die Hersteller darüber hinaus, die Ursachen proaktiv anzugehen. Dieser Einblick versetzt die Hersteller in die Lage, die Ursachen von Ineffizienzen zu beseitigen und ein nachhaltiges Wachstum und eine höhere Produktivität zu erzielen.
Um dies zu erreichen, können Sie auch die Tools von Timly für eine bessere Anlagenverfolgung und ein besseres Wartungsmanagement nutzen. Die Echtzeit-Datenanalyse von Timly hilft Herstellern, versteckte Ineffizienzen zu finden. Dieser proaktive Ansatz ermöglicht es Unternehmen, bessere Entscheidungen zu treffen, die Arbeitsabläufe zu verbessern und die Rentabilität zu steigern.
Wie können Sie die OEE effektiv messen und überwachen?
Das Bild stammt von 6 Sigma
Die effektive Messung und Überwachung der OEE erfordert standardisierte Verfahren und Werkzeuge für genaue Berechnungen und kontinuierliche Verbesserungen. Sie können dies erreichen, indem Sie sich auf drei kritische Faktoren konzentrieren: Verfügbarkeit, Leistung und Qualität. Durch die Überwachung dieser Aspekte an Schlüsselpunkten Ihres Produktionsprozesses können Sie wertvolle Erkenntnisse darüber gewinnen, wo Ineffizienzen auftreten.
Aber wie oft sollten Sie die OEE messen?
Nun, Sie können täglich messen, wenn es um wichtige Geräte geht. Wöchentlich, um allgemeinere Trends zu ermitteln, und monatlich für langfristige strategische Erkenntnisse.
Allerdings sollten Unternehmen bei der Überwachung der OEE einige häufige Fehler vermeiden, z. B. veraltete Benchmarks, das Ignorieren kleinerer Ineffizienzen oder das Übersehen von Mängeln. Dies kann ihnen helfen, genaue und aussagekräftige Auswertungen zu erhalten.
Die Überwachung in Echtzeit ist ebenfalls entscheidend, um nachhaltige Verbesserungen zu erzielen. Timly stattet Hersteller mit Tools aus, die für die OEE-Verfolgung in Echtzeit, vorausschauende Wartung und Datenanalyse entwickelt wurden.
Auf diese Weise können Unternehmen die laufende Leistung überwachen, Engpässe erkennen und sofort Korrekturmaßnahmen ergreifen. Um zu sehen, wie es funktioniert, buchen Sie noch heute ein unverbindliches Online-Meeting mit uns oder starten Sie direkt mit Ihrem kostenlosen Testkonto.
Häufig gestellte Fragen zur Gesamtanlageneffektivität
Was ist die Gesamtanlageneffektivität?
OEE ist eine umfassende Kennzahl, die in der Fertigung zur Messung der Effizienz verwendet wird. Sie bewertet die drei Komponenten Verfügbarkeit, Leistung und Qualität, um festzustellen, wie effektiv die Anlagen im Verhältnis zu ihrem vollen Potenzial genutzt werden.
Was sind die häufigsten Herausforderungen bei der Erreichung einer hohen OEE?
Zu den allgemeinen Herausforderungen bei der Erzielung einer höheren OEE gehören ungeplante Ausfallzeiten, unterschiedliche Bedienerpraktiken und Unstimmigkeiten bei der Produktqualität. Unternehmen können diese Herausforderungen jedoch überwinden, indem sie in fortschrittliche Tracking-Tools, bessere Schulungen und robuste Wartungsroutinen investieren.
Für Sie empfohlen:
Buchen Sie eine kostenlose und unverbindliche Online-Demo oder erstellen Sie direkt Ihr kostenloses Testkonto.
Sie sind noch nicht so weit? 10 Tage Testzugang zur Software ➟