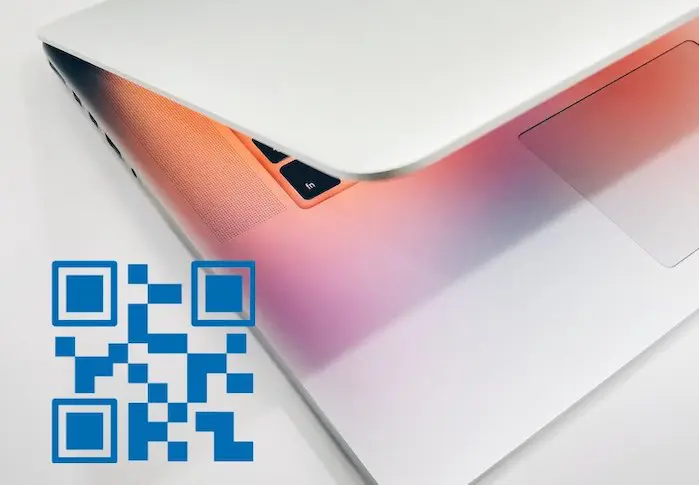
What Is an Inventory Number?
The inventory number is small and inconspicuous, but it has great significance. The number of your asset allows an object to be clearly identified. Without it, a lot can quickly go wrong because it ensures order and traceability. For example, if you find a piece of equipment in the workshop in the morning without an inventory number, you don’t initially know who is going to use it today or what its condition is. You have to rely on a colleague who happens to come by and knows more.
On this page you can read everything you need to know about object numbers and how software can simplify inventory in your company.
Timly in use at a construction site
What Are Inventory Numbers Assigned For?
Of course, every object and every licence has a designation in itself. But this can occur several times in a company or even in a department. For example, you may own three drilling machines of a certain model or twenty one-year licences for a CAD software. An inventory number that occurs only once, on the other hand, can be compared to a book signature in the library or the identity card number of citizens.
If each inventory object is given its own unique number, you can keep track of the inventory in a professional way. Finally, the approach with object descriptions has limitations and is only suitable for really small businesses. For clear identification of your inventory items, assign item numbers. These can generally consist of numbers, digits and special characters. However, once you have decided on a scheme, you should follow it continuously.
Typical inventory software can be set to automatically assign the asset number. When a new inventory object is entered, a suitable sequential number can therefore appear automatically that fits into the previous number structure scheme. In principle, an inventory number can appear on paper lists or in Excel tables. But these classic procedures have disadvantages that you no longer have to accept in times of mobile apps and cloud-based software.
After all, inventory management is far from done with attaching the number to the object. For fast and convenient management, the unique object numbers must also be recorded and used in an efficient inventory system. Such a well thought-out overview in inventory management reduces equipment losses and breakdowns, so you should by no means forego the assignment of clearly assigned object numbers.
Use of the Inventory Number: Example Construction Industry
Unique inventory numbers are the key to successful tool management. Thanks to labelling the company’s own inventory objects with specific numbers, many failures and losses as well as unnecessary search efforts can be avoided.
(No credit card required)
Central inventory management
Individual set-up
Assign inventory
Integrated barcode scanner
Maintenance & service management
Track performance & defects
User & role administration
Record GPS locations
Some construction companies already use classic labels with an item number on the tool. This number has to be found on the magnetic board or in Excel tables during administration. However, especially long object numbers in large companies can be difficult to read by eye. There can be number spinning when reading and comparing in the digital table or on the magnetic pin board in the warehouse. You quickly push the magnet into the wrong column or catch the row with a similar but wrong number.
So that the grinder or the ladder is not accidentally assumed to be in another employee’s trolley, electronic recording of the object number can help. If the number is integrated in the QR code, for example, you only need to scan it with your smartphone or tablet when you borrow or return a tool.
With good inventory management software, the asset number provides access to the full lifecycle tracking of the tool or vehicle. After purchase, a unique item number is assigned and performance data is recorded, and operating instructions and maintenance dates may be stored. In future, every employee will be able to scan the inventory number and access this data.
This makes it easy to check on the construction site whether accessories for the tool used are available in the company. Questions about the technical data of the tool or its age can now also be clarified while on the road.
Asset Management Software in Use by Our Customers
The Timly software is continuously evolving to meet the needs of our customers. In various success stories, we show you how Timly optimizes processes in companies, thereby saving significant effort. With Timly, inventory management becomes child’s play.
Optimized Device Management With Innovative Self-Inventory
SodaStream is the world market leader for water sparkling systems for domestic use and has a lot of IT equipment at its various locations. Many colleagues now work from their home offices. A digital solution for the efficient management of IT end devices became necessary...
Panasonic x Timly: Driving Technological Innovation
One of the most remarkable aspects of human ingenuity is our ability to innovate. Innovation is embedded in the DNA of consumer electronics giant Panasonic, which has diversified into a number of sectors, from heavy industry to construction...
Manage Video Equipment Efficiently Without Much Effort
The Hamburg media company always does outstanding journalistic work and is characterized by independent reporting. In order to maintain journalistic quality, the teams work with highly specialized devices – these need to be managed efficiently...
Smart City Asset Management – Timly in Use at DIGOOH
The core business of DIGOOH Media GmbH in Cologne is to manage digital city light posters (DCLP) for outdoor use in various cities in Germany. The challenge here lies in making the client’s communication message always available at the right time, in the right place...
(No credit card required)
When it comes to inventorying furniture, vehicles, licences, equipment or tools, even companies in other sectors still like to rely on analogue tools or digital lists that are only available on certain desktop PCs. Thus, all employees always have to go to a special room first for inventory management. But if the inventory is so hard to reach, the temptation to enter changes later increases.
If a staff member borrows a piece of equipment from a colleague “for a short time” and does not want to go down three floors to the room with the inventory list, for example, the chances increase that she will end up forgetting about it or lending it to someone else. If another colleague wants to use the same device, she looks in the inventory list but only finds the outdated location. So there is an inventory number on the device, but in order to discover it, one would first have to ask around in the company for the actual location.
With mobile inventory management software, on the other hand, capturing the inventory number is quick. The indication that something is being borrowed or returned is only a few “clicks” away on the work mobile phone. Because helping to keep the inventory cloud database up to date is so easy with software such as Timly, full transparency on the whereabouts and status of inventory items is more likely to be achieved than using rigid, traditional tools. A digitised inventory accessible via a cloud makes many work processes more efficient.
Assigning Inventory Numbers Sensibly With Modern Software
Reading numbers yourself and typing them out manually was yesterday. Today, labels with scannable QR codes are used, in which the item number is integrated. These are stuck on equipment, furniture, vehicles, etc. to be scanned with a mobile phone or tablet when a change to the inventory object is to be recorded. As a Timly customer, you can use the mobile inventory app, which is available for iOS / iPhone / iPad as well as for Android devices.
The number allows information about objects to be called up in the Timly Inventory software
And this is how you manage your stocks efficiently with inventory numbers:
Overview of the inventory at any time and from anywhere
Compatibility with mobile devices such as smartphones or tablets
Integrated barcode / QR code scanner
Easy mass inventory possible
Assigning the inventory to individual persons or places
Store files, documents or even contacts
GPS location tracking incl. location history
Similar Blog Posts:
Book an online demo - free and without obligation - or create your free trial account directly.