Steaming Full Speed Into Digital Transformation
Looking back over the past two centuries, it’s hard to deny the instrumental role railroad construction has played in transforming and shaping our world. Among the drivers of change in the railway industry in Europe today stands Germany’s Willke Group: an innovator and leader in railway construction. Join us as we explore how Willke has successfully implemented cloud asset tracking with Timly to maintain its fast track to digitalization.
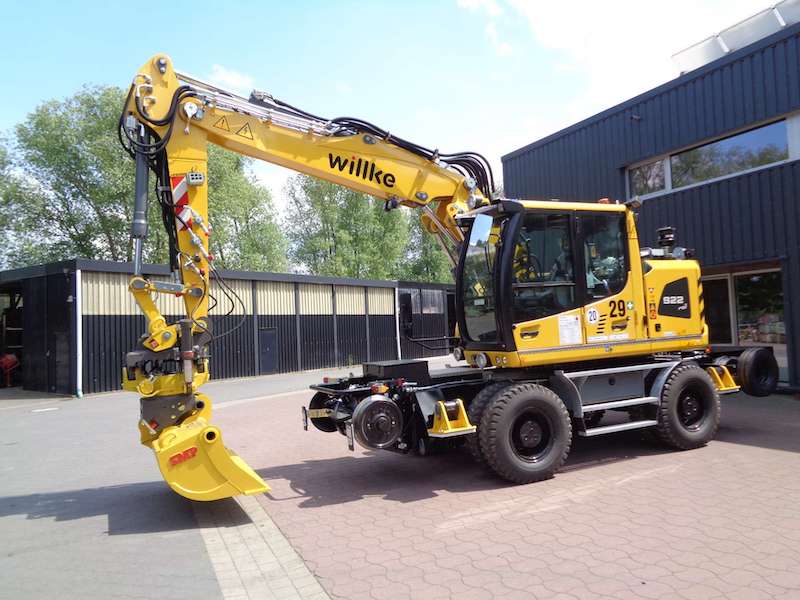
Willke Group
Founded
1979
Headquarters
Countries
3 (across 13 locations)
Industry
Railway Construction
Number of Employees
500
Assets
6,000 objects
The Challenge: Keeping Track of Assets Across Locations
Willke boasts a large, modern machinery park equipped to handle the most demanding railway construction projects.
Established nearly 50 years ago, Willke has evolved from a family-owned business into a corporate group with multiple specialized divisions and a team of 500. Technology has always been central to its vision and growth. When it came to its inventory management, as with many companies, Willke relied on a combination of spreadsheets and ERP systems, and for many years this approach served well. However, with the expansion of the Group into 7 specialized divisions of railway construction, managing its extensive inventory of machinery, tools, and equipment became increasingly complex. Running projects across multiple locations, where items needed to be deployed and returned daily, only added to this complexity.
In railway construction where tools and machinery are central to day-to-day operations, any delay in locating, checking out and returning items can quickly turn from an inconvenience into a serious obstacle, impacting workflows and productivity. In the long-term, an inadequate inventory management system can even significantly impede a company’s ability to grow and scale. This consideration, coupled with the need to ensure accurate, accessible and always up-to-date inventory data, led Willke to Timly in 2021. As Jost Cors, Head of Digitalization at the Willke Group, explains:
“ERP systems are powerful, but often hard to learn and require costly licenses. Excel spreadsheets provide a variety of useful functions, but without a solid business logic they are prone to errors – and key personnel are a bottleneck resource.”
The Solution: A Platform for Single Inventory Tracking
What was needed was a modern inventory management solution that’s aligned with the Group’s forward-thinking approach and growth trajectory. For this, the new asset tracking system needed to be robust yet flexible. This would enable Willke to organize, track, and manage its vast array of assets across multiple locations, at the same time empowering its users to readily adopt the tool and to access and use it from anywhere. Cors states:
“Our first use case was and still is the management of asset master data in a dedicated, easy to learn and use asset tracking system. This is because we’ve come to recognize that clean master data is the prerequisite for other use cases in our company.”
Timly stood out with intuitive functionalities, cloud-based accessibility and a high level of customization. This allows Willke to organize their asset data in the way that makes most sense to the Group, and to roll out the solution to other areas as business needs evolve. Barcode technology makes checking out and returning items as easy and quick as a few clicks. Timly QR code labels are attached directly onto equipment, enabling Willke’s users to scan items directly with their mobile phones and instantly update the whereabouts of equipment in the inventory management system.
Moreover, users can directly report any equipment malfunction directly in Timly and can request help for other asset-related issues. This is possible because Willke is using the ticketing system feature in Timly to integrate support desk activities with inventory management. This, coupled with the ability to plan, execute and document both routine and ad hoc maintenance and inspection schedules, means Willke can ensure its equipment is always operational and in optimal condition.
With Timly’s QR labels, Willke ensures that checking items in and out is easy, quick, and reliable.
Most used functions:
Maintenance Planning
Willke boasts a vast and modern fleet of machinery, tools, and equipment that require regular maintenance and inspections. With Timly’s maintenance scheduler, they can plan, execute, and document all related activities.
Staff Training Records
Operating in a highly regulated sector where workplace safety is paramount, Willke makes great use of Timly’s staff training record capabilities to ensure its staff are trained, qualified, and certified.
The Result: Complete Oversight and Strategic Insights
Willke’s high safety standards include regular maintenance and routine inspections of its machinery.
Moreover, Willke was also able to remain in the driver’s seat and ahead of important safety and compliance matters, from maintenance and inspections to staff training and certifications. Specifically with regards to the latter, Willke provides a great example for how to effectively leverage the employee training and skills records management feature in Timly. By scheduling training for staff directly in Timly, Willke can maintain a complete overview of past and upcoming training events for individuals and groups of staff. The Group meticulously organizes its staff certifications and qualifications in categories, giving managers a simplified overview how many staff have had which training, what training is due, and so on. Asked about the most useful features in Timly for Willke’s use case, Cor’s reply was:
“The deadline and qualifications overviews because they make it extremely easy to monitor expiring deadlines, expiring qualifications, to schedule maintenance, inspection measures and training courses way before they are due, and we can provide managers with all the information they need on the current status in a really simple and summarized form.”
Willke’s approach to its digital asset tracking speaks of its evidence-based approach and its placing a high value on data driving its planning and actions. The visibility over their assets in Timly allows them to make informed decisions about asset maintenance, procurement, and deployment, and they can thus optimize the return on investment for their extensive equipment inventory.
Switching to a cloud inventory management system did more than just give Willke a tool to manage its inventory from anywhere – Willke was able to decide exactly how to implement Timly for its use case and unique needs. As Cors points out, another positive discovery with Timly was “the customization possibilities and I have to say excellent usability despite the extensive functionalities in basically all parts of the software, that was a surprise.”
Willke is highly valued at Timly, appreciated by the team not only for the great working relationship but also for the Group’s drive to innovate and pioneer new paths. We are proud to support their asset tracking and inventory management efforts and look forward to continuing this successful journey with them.
Image Rights: ©Willke Group