Digital Into the Future: Timly in Use at 250 Euromaster Service Locations
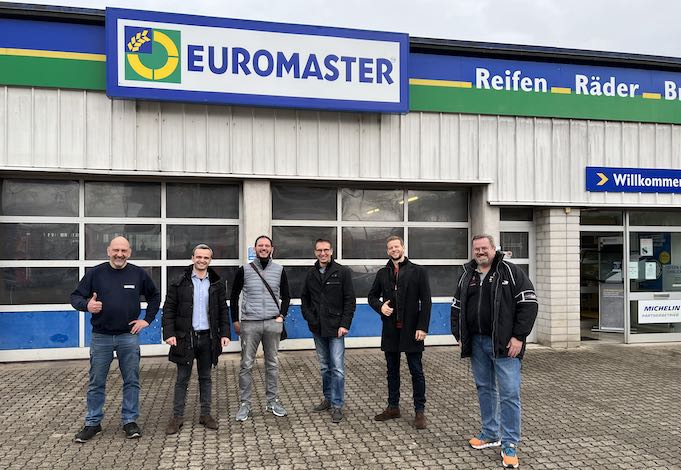
Euromaster GmbH
Founding year
1991
Locations
335
Revenue
~245 mln €
Industry
Tire & car service
Employees
~1,900
Assets
The Challenge: Minimise Effort Through Improved Information Status
However, data quality is extremely important to Euromaster, because “TÜV” & co. carry out regular audits at the service locations. If the right information cannot be provided at the right time, such an audit can paralyse an entire branch for several days. This is mainly about checking equipment for safety and suitability, checking documentation of services & repairs, related documents, invoice control and many more.
The Solution: Decentralised Data Collection Provides a Centralised Overview
Data Import
It quickly became clear that Euromaster would have to make an initial and one-off effort to prepare the data. However, this is important so that the asset data can also be imported cleanly into the Timly system. In the process, categories will be matched with each other and templates for data entry will be created for all locations. The aim is to import all details such as serial numbers, machine designations, conditions and locations of the inventory correctly.
In future data recordings, it will be important to merge item information. The decentralised recording of repairs & services at the individual locations (via the inventory app) can also be significantly simplified by the Timly software through standardisation.
Via the QR code labels on the devices, employees can quickly view and record information
Manage Maintenance & Services
The Maintenance Planner & Service-Management module in Timly allows future repairs to be managed more efficiently. The integrated deadline planner makes it possible to keep track of the necessary safety inspections of the numerous devices and machines at a central point (compliance!). Here, a differentiation is made between time-dependent and time-independent occurrences, such as weekly, monthly and quarterly deadlines.
Damage reports to service partners are to be automated, which is a challenge: The Timly software must make the numerous service partners available for the different categories and select who is responsible for which damage. Warranty periods must be kept in view at all times.
Document Management
In addition, there is an efficient document management for the assets. Of course, there are dozens of digital files for the devices used at the locations, such as manuals, safety instructions, protocols and invoices – accumulated over several years. These can be stored in Timly for each device and made accessible depending on access rights.
User Role Concepts
In addition to the “power users”, it is important for Euromaster to work out individualised user authorisations and to create role concepts for the different types of employees. Since decentralised data entry into the Timly system is planned, problems such as “accidental deletion” and “incorrect entry” should be prevented at all costs. The normal user at the site must be given individual authorisation to add serial numbers and barcodes to machines, as well as to enter standard inputs.
Mainly Used:
Maintenance planning
With a centralised overview of service management and operations, management can get a real-time picture of the maintenance status of all fixed assets.
Ensure compliance
With more visibility of data, operations and documents on their inventory (tools & machinery), Euromaster achieves greater efficiency.
Result: Individualisation of the Product Roadmap
The complete implementation of the Timly software at the approximately 250 locations is planned for the summer of 2022
In the course of the discussions and application on site, the importance of further ideas and insights that emerge from the use of Timly also became clear very quickly. Through the Rooms & Containers function, Euromaster will be able to digitally map the local conditions per location in the future and thus make much more efficient planning efforts:
How many square metres does which location have?
What is the clearance height of the garages?
Which special lift platforms are in use at which location?