Timly x Bayer: The Science of Inventory Management
How many times in your life have you read or heard the name “Bayer”? Quite a few, most likely. This innovative company is now ingrained in the collective consciousness and history for its contributions in a wide variety of fields. At Timly, we’re happy to make the daily operations at the chemical development department within the Bayer Supply Center Wuppertal simpler by streamlining parts of their inventory management.
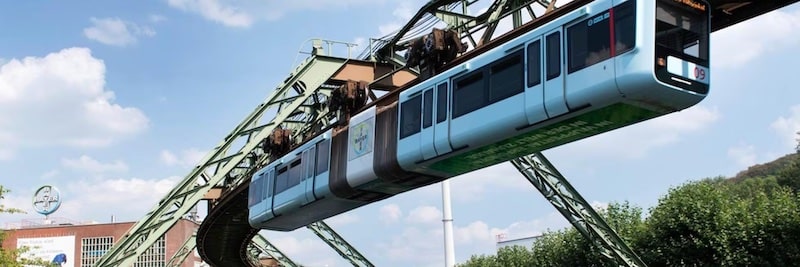
Bayer
Founding Year
1863
Headquarters
Leverkusen, Germany
Countries
80
Industry
Life Science
Number of Employees
99,723 (worldwide)
Assets
1,000
The Challenge: The need to streamline and modernize inventory management
Jan Wendel, Lab Technician at Bayer Supply Center Wuppertal
If you want a concrete sense of Bayer‘s impact on the world, it’s not hard to find… Just consider, for example, what the world would be like if this German company hadn’t invented Aspirin. This medicine, which seems commonplace today because it’s so deeply integrated into our lives, was quite revolutionary when it was first discovered in Wuppertal over 130 years ago.
Since then, the company has expanded across multiple sites and exported its products to numerous countries, driving countless advancements in pharmaceuticals, medical innovation, research and development, chemistry and more. To be and remain an innovative company, it is necessary to observe new developments, evaluate new solutions and move with the times. All processes that take place at the Bayer sites are cogwheels that must mesh perfectly. It is therefore also important to utilize the state-of-the-art solution in terms of inventory management processes. All with the aim of ensuring the delivery of medicines and thus patient health.
“In our chemical development department in Wuppertal we needed to find a solution to gain a better overview of our inventory. The goal was to unify and modernize processes to implement better working methods. It turned out that Timly was a perfect match.” (Jan Wendel – Lab Technician at Bayer Supply Center Wuppertal).
The Solution: Update to digitalized inventory management
And speaking of transformation, let’s get concrete: At the Bayer Site in Wuppertal new pharmaceuticals are researched and developed, and new active ingredients are produced. Therefore, they have numerous lab reactors, which are essential equipment in the daily operations of such an organization.
To start, the team in Wuppertal implemented a maintenance schedule for the lab reactors, accompanied by Timly’s digital checklist. Our software provides real-time insight into the lab reactor fleet, as well as information on their maintenance status. Timly’s multi-user capacity allows for widespread communication of lab reactor information among different teams.
The Chemical Development Department in Bayer Wuppertal has created a rich and comprehensive inventory database, with many customizable fields tailored to their specific needs. Thus, the team dedicated to these reactors can easily check key inventory information with a simple click: « Where is this equipment located? »,« Has maintenance been performed on this reactor? », « Who is responsible for such a tool? ». All these questions find their answers in Timly.
The teams also benefit from deadline management features, activity management, defect and damage reporting, asset allocation (to individuals or locations), and more. Jan Wendel (Lab Technician at Bayer Supply Center Wuppertal) summarizes: “Now, everybody has a faster overview of its devices in all labs, execute maintenance of the reactors and we have a digital solution.”
Most used functions:
Scheduling Maintenance
Timly’s digital maintenance planner empowers Bayer Wuppertal employees with an advanced solution for maintenance management, especially for their lab reactors.
Mobile Access
Our cloud-based inventory app is particularly appreciated by the team using Timly on their tablets. Information is centralized on a single platform, accessible at any time, from anywhere.
The Result: Ingenious & efficient inventory management
Implementing Timly as the inventory management platform for the Chemical Development department has allowed for harmonization and optimization of processes beyond their own teams.
Bayer Wuppertal reactors are fitted with Timly QR codes
« We have 100 lab reactors, managed by a dedicated team. To streamline our process, we’ve integrated a dummy user for this team into Timly. Now, whenever a new malfunction is reported, the team receives automatic notifications. » (Jan Wendel – Lab Technician at Bayer Supply Center Wuppertal)
Timly brings clarity and simplifies compliance by providing all essential inventory information on a single page, and by offering features that simplify and strengthen maintenance management.
“Timly is a great tool for easily managing all kinds of inventory and stocktakes.
It is intuitive and there is a lot of flexibility for how to manage your assets. ”
Jan Wendel (Lab Technician at Bayer Supply Center Wuppertal)
Image Rights: ©Bayer